The Challenge The aluminum industry faces significant challenges in reducing its carbon footprint while maintaining efficient and cost-effective production. Traditional systems often consume excessive energy, generate high emissions, and rely on substantial amounts of additives like AlF3. Storvik was tasked with delivering an innovative solution that addresses these critical concerns. Our Approach Storvik developed the […]
The Challenge
The aluminum industry faces significant challenges in reducing its carbon footprint while maintaining efficient and cost-effective production. Traditional systems often consume excessive energy, generate high emissions, and rely on substantial amounts of additives like AlF3. Storvik was tasked with delivering an innovative solution that addresses these critical concerns.
Our Approach
Storvik developed the ICON technology with a focus on energy efficiency, emission reduction, and process optimization. The approach included:
- Energy EfficiencyICON technology requires less energy, directly reducing the carbon footprint associated with aluminum production.
- Emission ControlThe system operates as a closed unit, significantly lowering harmful emissions released into the environment.
- Optimized Resource UsageThe technology minimizes the amount of AlF3 required, offering cost savings and reducing chemical dependency.
- Compact DesignThe compact system is versatile and can be seamlessly implemented on tapping vehicles or crane-based tapping systems, ensuring operational flexibility.
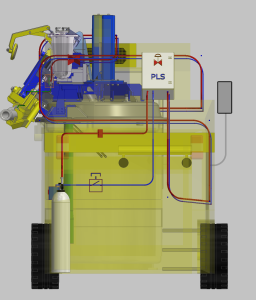
Out Outcome
Storvik’s ICON technology has set a new standard for sustainability and efficiency in the aluminum industry. Key outcomes include:
- Reduced Environmental ImpactLower energy consumption and emissions contribute to a significantly smaller carbon footprint.
- Cost-Effective ProductionOptimized use of AlF3 and energy savings improve operational economics.
- Flexible IntegrationyThe compact design supports easy adaptation to existing systems, enhancing practicality for diverse production setups.